Description of Findings
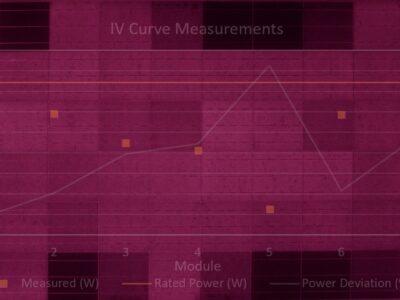
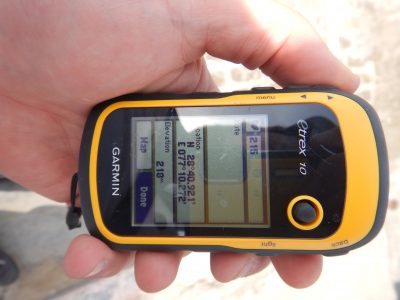
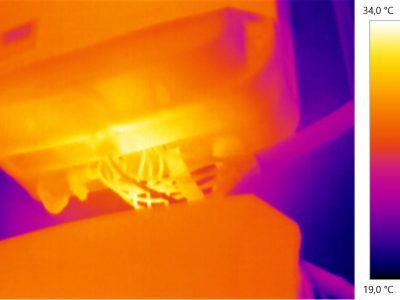
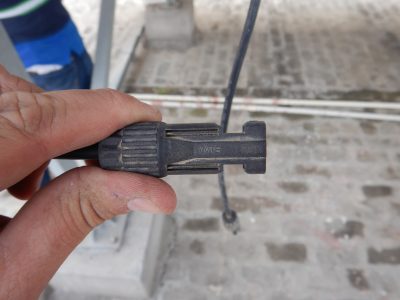
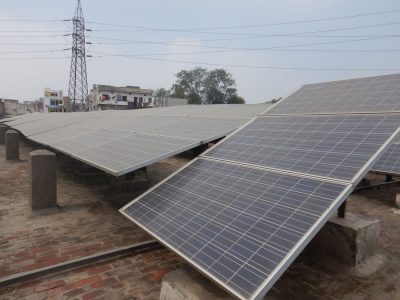
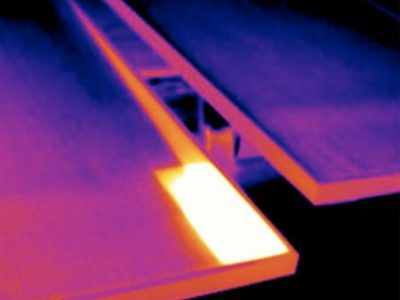
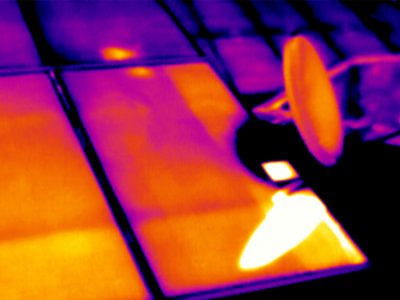
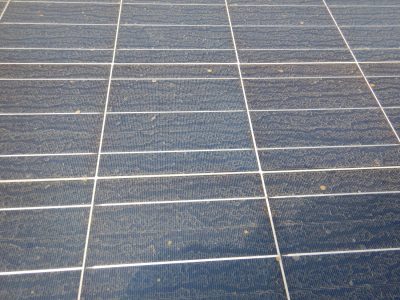

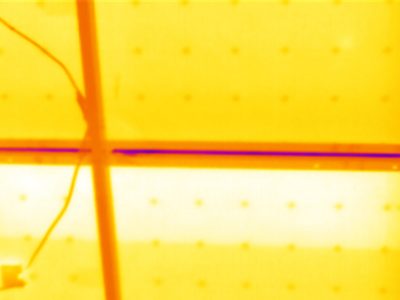
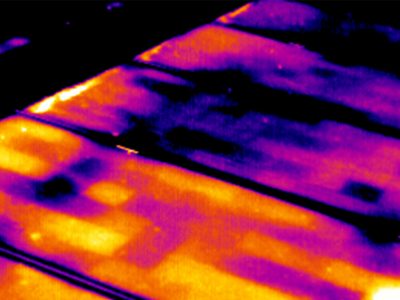
According to different logistic providers for PV modules, 15M+ solar modules are broken every year prior installation. PV Module damages are often due to shipping on fragile wood pallets and boxes with partial loads. Module handling, transport and installation require minimal understanding of the PV technology.
Even though these issues are known within the industry, mechanical effects in the modules, i.e., cracks, scratches, broken glass, are still a nuisance in project development, especially during transportation (Factory – distribution center – project site – mounting structure). New technologies have also brought new sources of cracking, (interconnect ribbons for 9+ Busbars (CEA), manual solar cell soldering, lamination for certain EVA films with weak moisture impermeability). Furthermore, environmental aspects such as as snow loads, strong winds and hailstorms could induce major cracks on the modules’ surface.
The majority of micro-cracks occurred in the range of low resonance frequency during road transportation (L. Chang, et al): diagonal cracks, parallel to busbars crack, perpendicular to busbars crack and branched cracks. Branched cracks are more likely to produce underperformance in the mid term when the cracked areas become isolated.
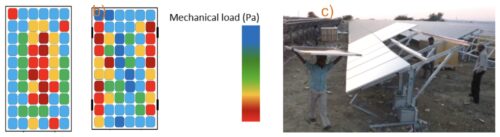
The PV modules are the core of a solar photovoltaic system. Hence, for the assurance of the Module quality of a PV plant, the best practices suggest performing in-factory supervision of production while PV modules are being manufactured. This includes experienced Quality Engineers deployed in the factory during production. The Engineers will supervise production to ensure that all required material, process and production controls are applied – and applied correctly.
When this process cannot be implemented or is not part of the scope or a Project, there are a few mitigation measures to uncover possible risks on an early stage of the projects. These are the so-called Pre-shipment Inspection, Post-Shipment Inspection (PSI) and Inspection During Installation procedures.
The Pre-shipment inspection is normally carried out on a sample basis and used to release modules for shipment (Manufacturing facility). During the Post-Shipment Inspection, a sample of modules is normally tested prior installation. Upon delivery of the modules to the Project site, and prior to the installation of the modules, Visual inspection (VI) and Electroluminescence (EL) imaging are performed once again. Here, the defect criteria defined in the supply agreement will be used (when available). During installation, the technical advisor will provide oversight of the installation of the modules and testing on a quantity of installed modules (VI and EL) and mounting structure (VI) to verify the quality of the installation work, including but not limited to: PV Module Handling & Storage and PV Module Mounting (EPC, different crews). Quality criteria as defined in the purchase is normally used, unless specified otherwise.
For the sites for logistics assessment, the main reporting should be focus on the evolution of the VI and EL failures in the modules from manufacturing, at warehouse (Intermediate delivery), upon arrival and after installation in a way that the 4 pictures evaluated are displayed so it is clear where the modules suffered most of the damages, i.e., Manufacturer/Warehouse – On-site delivery – After installation.
The purpose of this evaluation is to describe a common acceptance criterion for the Electroluminescence analysis (PI Berlin) for Poly-crystalline and mono-crystalline PV modules. PV Modules with critical defects are to be replaced after inspection by the owner/constructor, according to contractual criteria (with replacement modules being inspected under the same criteria).
Figure 18: Cracks: branched, broken small, crack cross, crack perpendicular, scratch, broken multiple (PI Berlin)
Then, a more superficial evaluation of the sites in general (mounting structure, cabling, shadings, etc.) was performed.