Site III.9
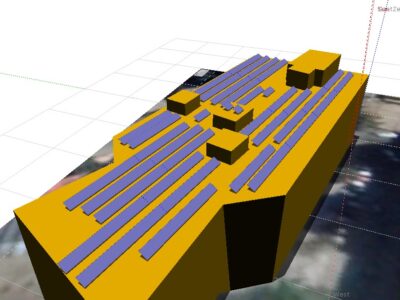
Site ID
III.9
Health
COD
2018
Nominal Capacity
499 kWp
Average Specific Yield
1292 kWh/kWp
Total Estimated Loss
21.4%
Possible Gain
15% to 20%
CAPEX, OPEX
0.9 ₹/Wp, 0.2 ₹/Wp/a
Expenditure / Energy
N/A
Abstract
The PV plant is affected by moderate soiling due to city pollution, near and microshading. Infrared inspection revealed warm cables, different electrical and temperature anomalies within the modules. Electroluminescence imaging exposed different module mechanical damages. It is recommended to (i) improve cleaning activities, (ii) replace modules exceeding the manufacturer’s guaranteed performance drop, (iii) conduct a string reengineering with individual MPPT assignments, based on EL imaging or IR inspection and (iv) replace modules with inactive cell strings. The estimated production boost caused by the retrofitting actions lies between 15% and 20%.
Main Findings
The remaining pillar beams (from the building) induce microshading on several modules.
The mounting system includes power snap fastening & grounding clips. Although the installation time is reduced, O&M activites are limited since individual modules, from inside of the table, cannot be removed.
Through IR inspection, a handful of modules with inactive cell strings were spotted.
Moving between module rows is usually done by crossing over the tables, i.e., walking on the modules. Thus, mechanical stress is inevitable (cracks and broken cells). The cracks could also have been initiated during handling and installation.
Cabling installation failures at string level, such as hot cables at the inverter inputs, inaccurate soldering or loose connectors, were detected.
Impact on Performance
Heavy Soiling
Soiling measurements were conducted via short circuit current reduction and nominal power, before and after cleaning, with irradiations higher than 1000 W/m2. The estimated soiling factor is in the range of 4- 6.2%.
Estimated Loss
4%-6.2%
≈ 5.1%
Near Shading
Due to near objects and microshading, the simulation estimates near shading losses of ca. 4.3% on system level.
Estimated Loss
≈ 4.3%
Cell Cracks
Based on the crack distribution and type found during the electroluminescence inspection, the module nominal power could be reduced by 4-8%. Furthermore, these types of cracks could eventually lead to inactive areas and higher power loss in the midterm.
Estimated Loss
4%-8%
≈ 6%
Inactive Cell Strings
Modules with inactive cell strings could underperform 33% to 66% depending on the amount of affected strings. The extrapolation of the inspected sample to the whole system leads to a loss of 6% on string level.
Estimated Loss
≈ 6%
Total Estimated Energy Loss
≈ 21.4%
Proposed Solutions
The remaining pillar beams shall be cut or bent to avoid microshading.
A weather station, or at least an irradiation sensor on the module plane (GTI), shall be installed so that the performance ratio of the system can be properly calculated.
Manual cleaning shall be implemented and scheduled based on the results of a soiling study that adjusts the cleaning needs to each season.
Modules with similar amount of cracks shall be re-grouped in the same string or at least assigned to one MPPT. The grouping will be conducted, ideally based on EL imaging, otherwise through IR inspection with high irradiation levels and after cleaning activities.
Modules underperforming above the warranty conditions shall be replaced. If the replacement is not possible, the modules shall be re-grouped in power classes within the same string and assigned to individual MPPT in combination with the amount and type of cracks.